Cast iron pipes are made by cutting and forging grey cast iron into a round shape with a hollowed center. Back in the day, this piping system was the standard for transporting gas, sewage, and water in residential and commercial properties. Despite the new materials, cast iron pipes are still used in commercial construction. However, with time, they can fall apart or corrode with waste and wreckage without maintenance and cause various plumbing problems like leaks, slow water drains, and stoppages that may require a costly repair.
Cast Iron Pipes Video
Property managers, if you have slow water drainage, frequent leaks, and stoppages… Let me show you one likely culprit. These are cast iron pipes.🚰 They’re sturdy when new, but over time they corrode and crumble which makes them ticking time bombs beneath your property. On top of that, they tend to get packed with decades of debris which causes backups, more leaks, and mold growth which can lead to potential health issues. 🤢
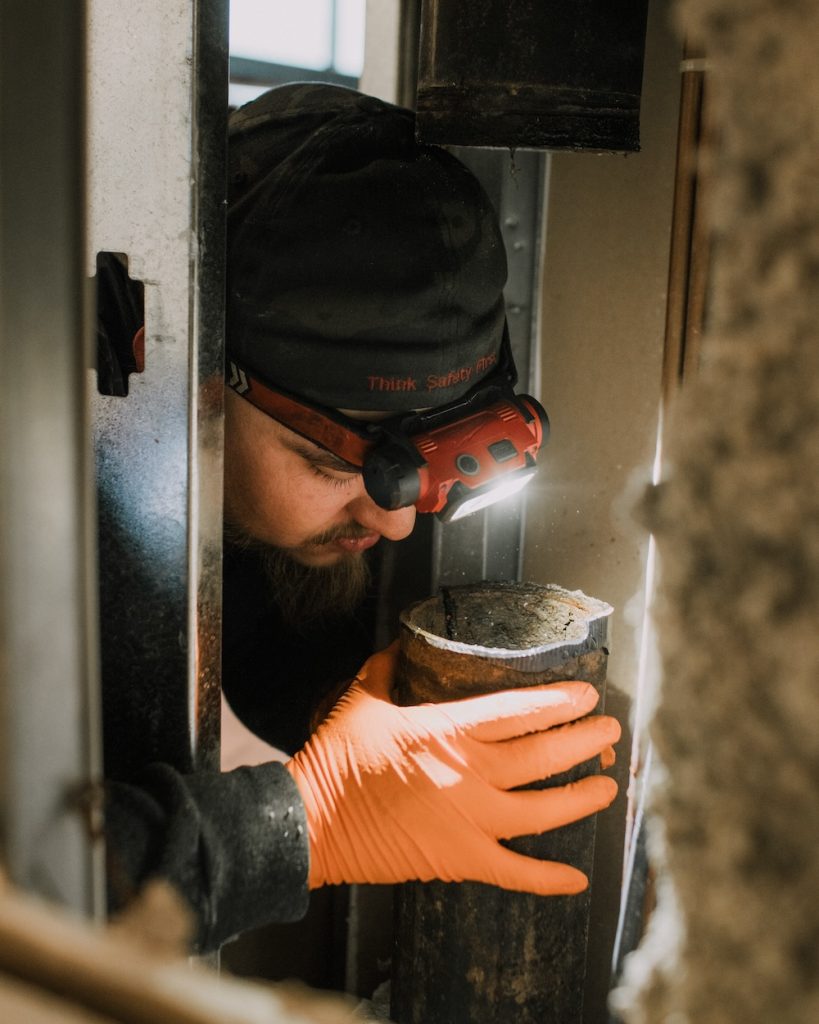
Here’s our recommendation:
Make sure you’re getting your plumbing system regularly inspected and maintained by a qualified plumber, that way we can prevent costly property damage, and recommend exactly when your cast iron pipes need to be replaced entirely.
History of Cast Iron Pipes
The cast iron pipes were first used in Versailles, France, in 1668, under King Louis XIV’s rule. A 15-mile long cast iron main was built from Marly-on-Seine to the palace and surrounding areas for the supply of water.
Interesting Fact: This system still functions after more than 300 years of service.
In the US, cast iron piping was imported from England and Scotland to supply water and gas to the larger cities of the Northeast. The first foundry that manufactured cast iron pipes in the US was established in Weymouth, New Jersey, in 1832; Pennsylvania and New York followed suit. By 1880, production spread to the Midwest and South.
During this time, cast iron pipes became the standard for water distribution, sewage, and stormwater systems because of improvements in casting and mold technology. This led to better-quality pipes with fewer defects, which still function today in many older cities.
But in the era between 1950 and 1975, new technology (ductile iron, PVC, PEX, and other plastics) emerged that replaced the use of cast iron pipes.
Different Types of Cast Iron Pipes
Several types of cast iron pipes are available, each for a different use:
Service Weight (SV)
SV cast iron pipes are known for their durability and can be used in residential and commercial plumbing systems to handle normal waste and venting applications.
Extra Heavy (XH)
Thicker than SV pipes, Extra Heavy cast iron pipes (XH) are suitable for applications that require additional strength, like high-rise buildings or areas with heavy traffic loads.
Hub and Spigot
Hub and Spigot cast iron pipes have a bell-shaped (hub) end and a plain (spigot) end. The spigot end fits into the hub end of the adjacent pipe, and the joint is sealed with molten lead or a rubber gasket.
This traditional cast iron pipe is really tough and many property owners used it in older plumbing systems. Although less common today, you may still find it in many existing infrastructures.
Hubless (No-Hub)
Hubless cast iron pipes, also known as No-Hub pipes, do not have the traditional bell-and-spigot ends. They are joined using stainless steel clamps and neoprene gaskets.
Not only this cast iron type is easier to install and maintain, but it also allows for more flexibility in tight spaces.
Coated
Coated cast iron pipes have an additional layer of coating, i.e., epoxy, cement lining, or other materials, for better resistance to corrosion in coastal areas or industrial settings.
Pros and Cons of Cast Iron Pipes
Pros:
- Durability: At least 50 to 70 years of operational life.
- Strength: Hard outer iron shell for high tensile strength.
- Noise Reduction: Acoustic dampening properties.
- Heat Resistance: Ability to bear temperatures of up to 650 °F.
- Low Maintenance: Requires drain cleaning (occasionally) for the removal of debris.
Cons:
- Weight: Heavy and requires a stronger support system.
- Corrosion: Rots from Inside out by years of hard water leading to clogged, slow drains, sewer backups, infestations, water damage, and more.
- Cost: Higher purchase, transport, installation, and repair costs than other alternatives.
Common Applications of Cast Iron Pipes
- Drainage and Waste Systems: Effectively handle sewage and grey water without deteriorating quickly.
- Vent Systems: Ideal for vent systems in multi-story residential and commercial buildings because of excellent sound-dampening properties.
- Underground Installations: A preferable choice for main sewer lines and storm drains due to their strength to withstand soil pressure and surface loads from traffic above.
- Fire Suppression Systems: Serve as a reliable channel for water delivery in fire suppression sprinkler systems.
- Retrofit and Repair: Used in retrofit and repair projects for older buildings to match the existing cast iron infrastructure for durability.
Comparison with PVC and Copper Pipes
PVC and copper pipes are the best replacements for anyone looking to replace their cast iron infrastructure in residential or commercial buildings. Let’s compare them below to help you decide which one best fits your needs.
Cast Iron Vs. PVC
- Strength: Under extreme conditions, PVC pipes are less durable than cast iron.
- Expected Life: PVC pipes last 25-40, which is far less than cast iron pipes.
- Corrosion Resistance: Cast iron pipes can corrode, but modern coating can fix this. On the other hand, PVC pipes are immune to corrosion.
- Initial Cost: Cast iron pipes have higher upfront costs due to material and labor compared to PVC.
- Installation: PVC pipes are easier to install than cast iron pipes because they are lightweight and can be cut easily.
- Maintenance: PVC piping maintenance is minimal, costs less, and it’s simple to replace damaged sections. However, cast iron repairs can be messy and may require a partial teardown of the property that can break the bank.
- Sound Insulation: Cast iron pipes have excellent sound-dampening properties, but PVC pipes require additional insulation to reduce noise from water flow.
Cast Iron Vs. Copper
- Strength: Both copper and cast iron are highly durable.
- Expected Life: Copper pipes usually last 50-70, but cast iron can stay operational for over 100 hundred years with proper maintenance.
- Corrosion Resistance: Cast iron and copper pipes can corrode, which can weaken their strength over time.
- Initial Cost: Copper piping purchase cost is higher than PVC but lower than cast iron.
- Installation: Copper piping is a bit easier than cast iron, although both require skilled labor.
- Maintenance: Copper pipes need regular inspection for leaks from corrosion but the repair costs are less than cast iron.
- Sound Insulation: Copper pipes are quieter than PVC but not as effective as cast iron.
Conclusion
Today, cast iron pipes are hardly used in new residential structures like homes and condominiums because they usually do not require plumbing pipes of such large size and strength. In commercial properties, they are still a preferable choice for sewer, drain, and water lines that have extra high pressure.
With care, you can make sure that cast iron pipes work for decades to come. However, if you want to replace them with new and cost-effective plumbing pipes, be sure to call a certified plumber service company. They can check your plumbing system and suggest other choices according to your budget and requirements.